Building upon our previous blog post that introduced the basics of the injection moulding process, we now delve deeper into optimization strategies that can enhance efficiency and quality. In this continuation article, we will explore techniques and considerations to maximize the benefits of injection moulding. By implementing these strategies, manufacturers can achieve higher productivity, reduce defects, and optimize overall performance
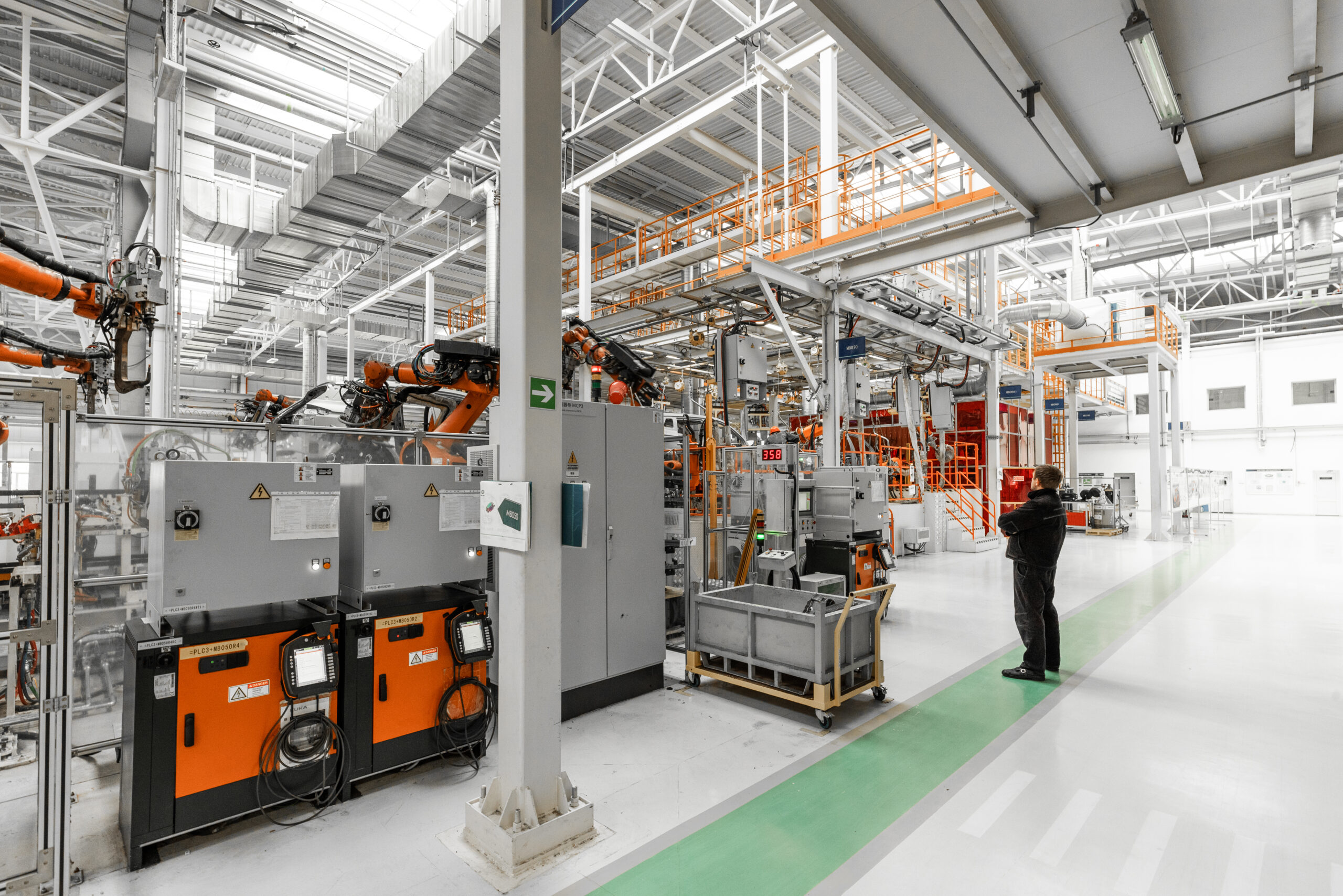
Strategies for Improved Efficiency & Quality
- Process Optimization
- Advanced Mold Design
- Automation
Process Optimization plays a crucial role in injection moulding, ensuring efficient and consistent production. Some techniques and factors are listed below:
- Injection Speed and Pressure: Adjusting the injection speed and pressure can impact part quality and cycle time. We will explore the effects of different injection profiles, such as fast-fill and slow-fill, in a separate article at a later time..
- Temperature Control: Maintaining precise temperature control during the injection moulding process is critical for material properties and part quality.
- Cycle Time Reduction: Minimizing cycle time is a key objective in injection moulding. This can be achieved by reducing cooling time through enhanced cooling techniques, optimizing mould opening and closing speed, and implementing automation for faster part handling.
- Material Optimization: Selecting the right material and optimizing its processing conditions can significantly impact part quality and productivity.
Mould design has a direct impact on part quality and manufacturability. Some advanced mould design strategies that can optimize the injection moulding process are listed below:
- Cooling System Design: Efficient cooling is critical for achieving consistent part quality and reducing cycle time. You may explore advanced cooling system designs, such as conformal cooling, baffle inserts, and optimized cooling channel layouts, that enhance cooling efficiency and improve part performance.
- Runner and Gate Design: Optimizing the runner and gate design can minimize material waste, reduce pressure drop, and enhance part quality.
- Moldflow Analysis: Moldflow analysis software enables simulation and optimization of the injection moulding process. It helps with the prediction of potential part defects, optimization of gate locations, and assessment of material flow behavior.
Automation and digitalization are transforming the injection moulding industry.
- Robotic Systems: Deploying robotic systems for tasks such as part handling, assembly, and quality inspection can improve process efficiency, reduce labor costs, and enhance overall productivity.
- Data-Driven Manufacturing: Leveraging data analytics and real-time monitoring systems can provide valuable insights for process optimization and quality control.
- Smart Manufacturing: The concept of smart manufacturing integrates automation, connectivity through Industrial Internet of Things (IIoT), and data exchange to create a highly efficient and responsive production environment.
By implementing the above strategies, manufacturers can unlock the full potential of injection moulding. The continuous pursuit of efficiency, quality, and innovation ensures that this manufacturing process remains at the forefront of modern production techniques. In our next blog post, we will make an attempt to dig deeper into some of the techniques listed above.
Get in touch
At PBC, we transform ideas into reality. With our advanced injection moulding capabilities, we can turn your concepts into tangible, market-ready products. Let’s collaborate!